Drilling fluid is used to aid the drilling of boreholes into the earth. Often used while drilling oil and natural gas wells and on exploration drilling rigs, drilling fluids are also used for much simpler boreholes, such as water wells. Liquid drilling fluid is often called drilling mud.
In drilling operations, solid weighting materials are commonly added to the drilling fluid to give sufficient density to the fluid to hinder inflow of oil or gas into the wellbore from the down-hole formation. Weighting material sag. i.e. sedimentation of weighting material from the drilling fluid, has been and is currently one of the biggest challenges within the drilling fluids industry as it can lead to well control problems, lost circulation, hindered running of casing/liner, insufficient displacement etc.
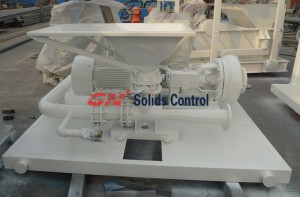
weighting material adding equipment
CALCIUM CARBONATE is Acid souble weight material.It is used to prevent fluid invasion of permeable zones, and to prevent loss of circulation during drilling, workover, and completion activities. CALCIUM CARBONATE is applicable in all drilling fluids, aqueous and non-aqueous. It can be used to prepare a pill for spotting purposes. is also used as an acid soluble weighting material for drill-in or workover fluids with a density of 14.0 ppg or less.
HEMATITE is for extremely high density mud.It is used to obtain mud weights in excess of 20.0 ppg in water based drilling fluids, 19.0 ppg in oil based drilling fluids, or any time that exceptional control is required of solids percentage for rheology control.
Barite is the most used weighting material, has a density of 4.1. It is used for increasing the density of fresh water, salt water, and oil based muds.
Barite is added through a hopper, GN designed Jet mud mixer is used for barite adding, it consist of venturi hopper and mixing pump. It can be used with the complete mud system, also it can be used separately.
Jet shearing unit is consist of venturi hopper and shearing pump, which can cut the big section into small pieces and add weighting material then mix them. It is commonly used in oil & gas drilling solids control system, usually it is installed on the weighting tank or mixing tank. Sometimes it is used together with decanter centrifuge.