Simply speaking, mud cleaner is shale shaker, desander, desilter assy, it is also called 3 in 1. GNZJ703 & GNZJ853 is the best choice for large treating capacity, large screen area mud cleaner, most of our clients use GN made mud cleaner before GN decanter centrifuge, this action can improve the performance of GN decanting centrifuge.
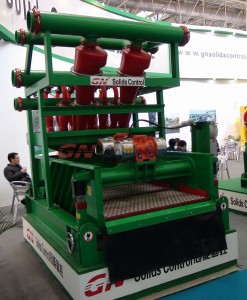
Mud cleaner maintenance including
1 vibration motor maintenance
(1)Clean dust on shell regularly
(2)Before operating, must check the bolts to confirm whether there is loose or not. Otherwise, we must screw bolts tight before running shaker
(3)Inspect the cable, whether there is wear, hold down, crushing, etc.
(4)the vibration motor should be under good lubrication during operation:
Motors before fixed on shaker, the bearing is filled with SKF specific lubricate grease, the temperature range is -40 ~ 200℃
2 shaker screen maintenance
(1)Before every shut off, the shaker should run without any load for 5-10 minutes, at the same time, use clean water to flush screen clean
(2)Every time finish operation, the shaker frame and screen should be flushed by water. Pls replace new screen or repair the damaged screen once it is found damage, otherwise large cutting may dropped into the clean mud and influence the following process.