The shale shaker is one of the main core equipment of the drilling mud solid control system. Recently, GN Solids Control received a batch of shale shaker orders from customers in Indonesia. After careful production and inspection, the shale shaker is now ready for shipment.
The GN Solids Control GNZS series shale shaker is the first stage of mud purification separation equipment in the mud system, and its importance is self-evident. The performance of the shale shaker will largely determine the mud purification performance and results of the complete solid control system.

In the design and manufacture of the GNZS shale shaker, we not only fully considered the working stability of the shale shaker, but also put a lot of effort into the ease of maintenance of the equipment.
First, the GN Solids Control shale shaker are all heat treated to withstand up to 8 G excitation forces.
Secondly, in order to ensure the good sealing performance of the shale shaker, GN Solids Control adopts U-groove at the bottom of the screen box and embedded rubber sealing technology. Not only makes the sealing effect better, but also makes the replacement of the sealing rubber more convenient.
GN Solids Control has developed three shale shaker to quickly change screens. Wedges, ratchet wedges and quick-press structures. Customers can choose which screen to press according to their own preferences.
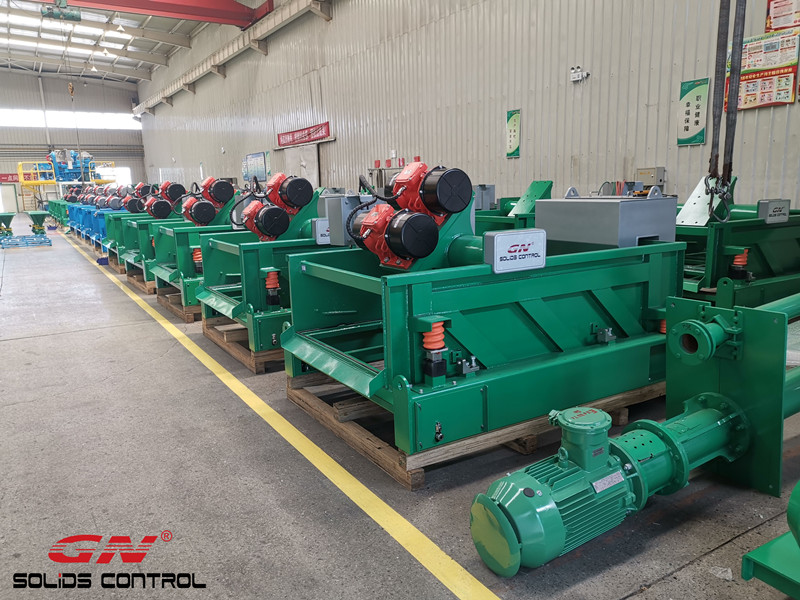
In addition to the process of quickly changing screens, GN Solids Control has also improved the damping rubber springs, so that the steel springs and rubber bushings are firmly combined, which not only improves the safety of the equipment, but also further reduces the wearing parts. quantity.
GN Solids Control shale shaker are primarily used for the purification of drilling mud. GN Solids Control shale shaker are widely used in oil drilling, trenchless and drilling waste management projects by replacing different types of models.
In order to achieve better mud purification, GN Solids Control technicians have also developed vacuum systems. The device can be connected to the last screen of the shaker. All GN Solids Control shakers are compatible with the installation of this vacuum screen system.
For more information on GN Solids Control conveyors, please feel free to contact us.