Recently, the oily sludge treatment system manufactured by GN Solids Control has been installed and debugged at a domestic customer and officially put into production, which has been highly praised by customers.
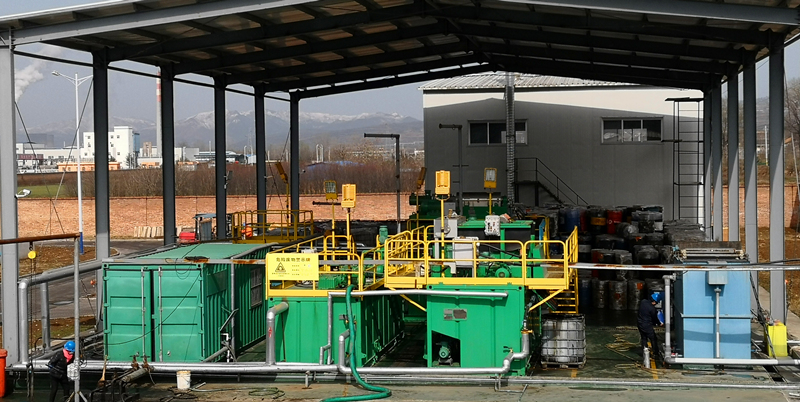
At present, due to various conditions such as different properties and working conditions of the oily sludge treatment system in China, few equipment manufacturers have consistent equipment. GN Solids Control has successfully developed a set of low-cost, high-quality system equipment through market exploration and technology research and development in recent years. The oily sludge is separated into multiple stages through this oily sludge treatment system, and finally the oily sludge is separated. Separated into oil, water, solid and other products. The separated oil can be directly sold to the refinery, and the water is repeatedly hot washed, and the oil content of the solid phase is controlled at about 1%-3%. The oily sludge reduction process is well completed.
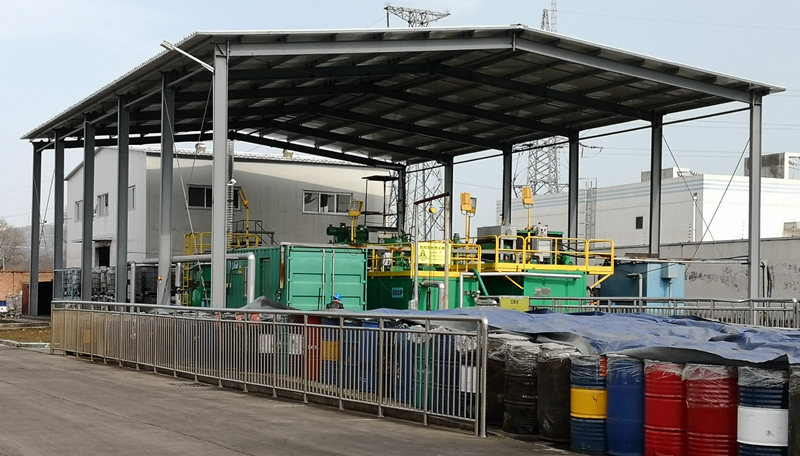
This oily sludge treatment system is GNOST-05A, which processes 5 cubic meters of modulated sludge per hour. The overall system includes a feed module and a sludge vacuum pump for sludge transportation; pre-mixing module-2 sets of heating pre-mixing tanks; dosing module- The three-compartment automatic dosing system and separation module-a decanter centrifuge and a disc separator, can well complete the continuous and automated work from the feed end to the discharge end. The complete system can be operated by only 3 people. The energy consumption is low, which greatly saves the cost per ton of oil sludge treatment.
Welcome everyone to contact the professional team of GN Solids Control, we will provide you with cost-effective solutions.