GN Solid Control is a well-known centrifuge manufacturer with state-of-the-art manufacturing processes and advanced domestic and international processing technology. The manufacturing precision of advanced imported processing equipment guarantee equipment in Taiwan, Germany and Italy has reached international standards. Mainly involved in the industry: drilling fluid solid control treatment, waste mud treatment, industrial wastewater treatment, oil slag separation, municipal sewage purification engineering, mining wastewater treatment, river dredging and so on. It is especially suitable for liquid-solid two-phase or liquid-liquid − it is suitable for liquid-solid separation where the solid particle size is small, the solid-liquid two-phase density difference is small (solid-liquid phase specific gravity difference >O.05), and separation is difficult. Solid, liquid-solid-solid three-phase separation, so it has been widely used in modern industrial processes, widely used in chemical, food, light industry, paper, mining and other industrial fields.
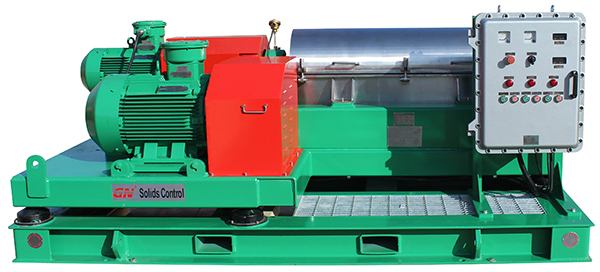
Some parts features and advantages:
1, auger
The main function of the screw feeder is to transport sediment and provide drainage channels. The structure, materials and parameters are not only related to the production capacity and service life of the centrifuge, but also directly affect the efficiency and separation effect of the slagging. The machine adopts a column/conical spiral, which consists of a spiral blade, a mandrel, a spiral-shaped end shaft, etc., and is supported on the drum-sized end cap by bearings on both ends of the journal, and the bearing is lubricated with grease.
Important parts are made of 2304/2205 duplex stainless steel.
The spiral blade is inlaid with replaceable wear-resistant alloy sheet, which shortens the service life of the pusher and reduces the maintenance cost. The acceleration cone of the mandrel is equipped with a replaceable alloy slurry outlet wear sleeve, mandrel. The acceleration cone is equipped with an acceleration strip to improve the treatment effect. The use of open-cell spiral blades improves the clarification effect.
2, the host base
It mainly plays the role of supporting and installing the whole rotary system. It also plays the role of vibration damping and vibration isolation together with the vibration isolator to reduce the propagation and influence of the vibration of the centrifuge to the external environment. The integrated steel structure welding machine base supports the whole rotating body (consisting of drum, spiral, differential, etc.) through the bearing seats at both ends, and the split-type sealed stainless steel collecting box covers the entire rotating body and is installed on the machine base. The elastic vibration isolator is installed at the bottom of the base, and the sensor cable is arranged on the bottom of the base. The main and auxiliary motors are arranged at one end of the base, and the inlet pipe is arranged at the other end. The whole layout makes the whole machine compact in structure, small in floor space and convenient in maintenance.
3, bearing housing
The bearing housing is divided into a large end bearing seat and a small end bearing seat. The bearing housing body is cast by cast iron, and the bearing inner ring is respectively mounted on the large and small end cover. The entire rotating body rotates in the two main bearings, and is lubricated by circulating oil. A special seal is used on the side.
In order to ensure the best separation effect for customers, GN Solid Control has been striving to improve production technology, improve design and provide customers with the most reliable products.
More question,welcome contact GN solids control