Oil well drilling mud conditioner are manufactured in our China factory.We provide you with competitive price,best solutions for drilling mud condition.
The present invention relates to additives or conditioners for oil well drilling fluids, and more particularly to a boron-chrome lignosulfonate drilling fluid additive or mud conditioner.
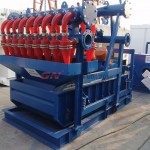
GN Solids Control design and manufacture Drilling Mud Conditioner utilizes a combination of hydro cyclones and a linear motion shale shaker to separate solids from liquid. The combination of hydrocyclone cones utilized is dependent upon the specific application of duty. Cone combinations typically consist of a few desander cones (10-inch or 12-inch) and several desilter cones (4-inch).
The most commonly used drilling fluids are aqueous dispersions of clay. The drilling fluid or “mud” is pumped down a hollow drill string, through the bit at the bottom, and up the annulus formed by the hole or casing and the drill string to thesurface. After reaching the surface, various operations are performed on the drilling fluid to remove the cuttings and formation material thereform. The drilling fluid is then treated with additives to obtain a desired set of rheological properties,and is then pumped back into the well in a continuous circulating process.
A satisfactory drilling fluid must have various desired functions, such as gelling during temporary work stoppage and other functions well known in the art, which contribute to the success of the well drilling operation. In order to accomplishthese various functions, it has been found necessary to incorporate certain additives in the drilling fluid. Modified lignosulfonates derived from spent sulfite liquor obtained from the pulping of woods have proven to be effective additives forobtaining the desired properties in drilling fluids.
These cones are mounted above the screen deck of the linear motionĀ shale shaker. The mud is fed first through the hydrocyclones, where it subsequently cascades down over the shale shaker. The remaining solids, including barite, are returned to the active drilling mud system.
The screens used on the shale shaker determine the cut point for the mud conditioner unit. When weighted mudĀ are used, shaker screens are selected in a manner that ensures that the majority of the weight material is returned to the mud system. Typically, API 170 screens (>82.5 to 98.0 microns) are utilized to reduce the amount of weight material discarded by the screens.
Drilling mud conditioner are widely used in petroleum oil and gas exploration industry, no-dig engineering, geotechnical engineering, mine, metallurgy, coal, hydropower and many other industries.GN drilling mud conditioning equipment can be used in both onshore and offshore oilfield project.HDD Horinzontal directional drilling mud system